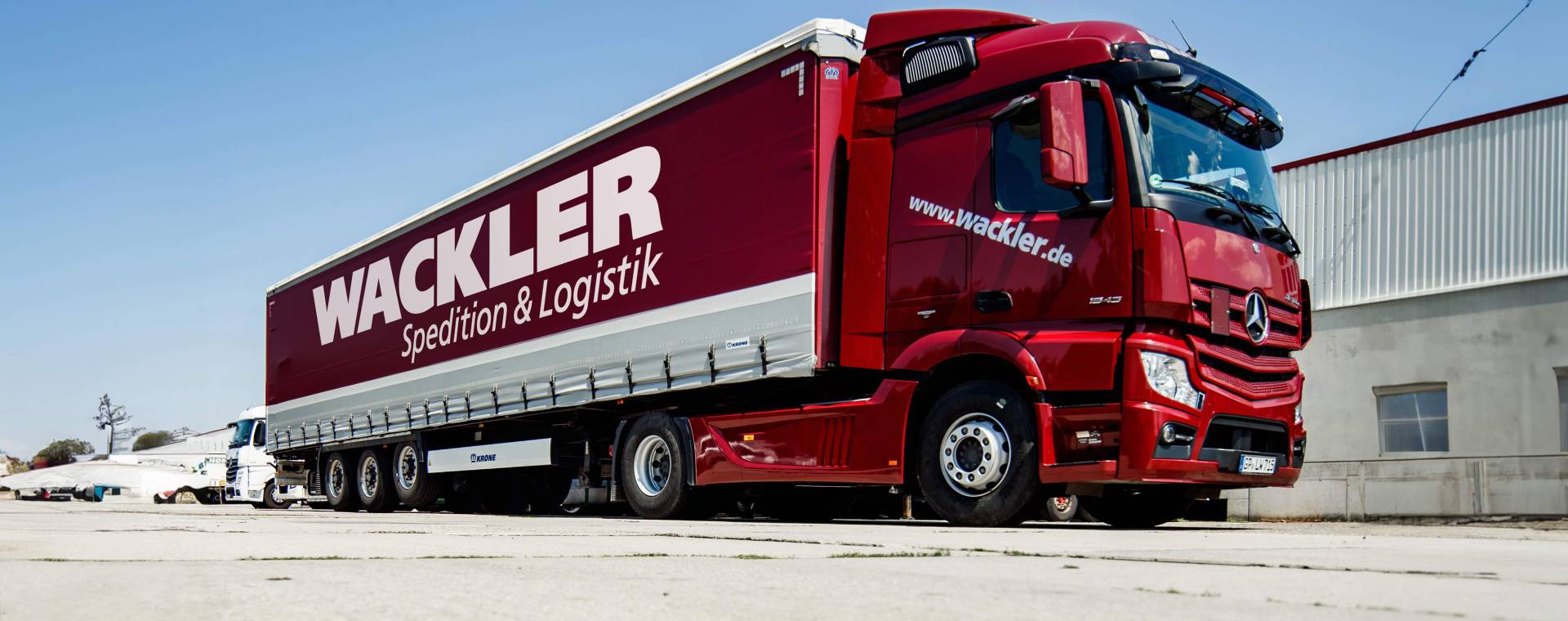
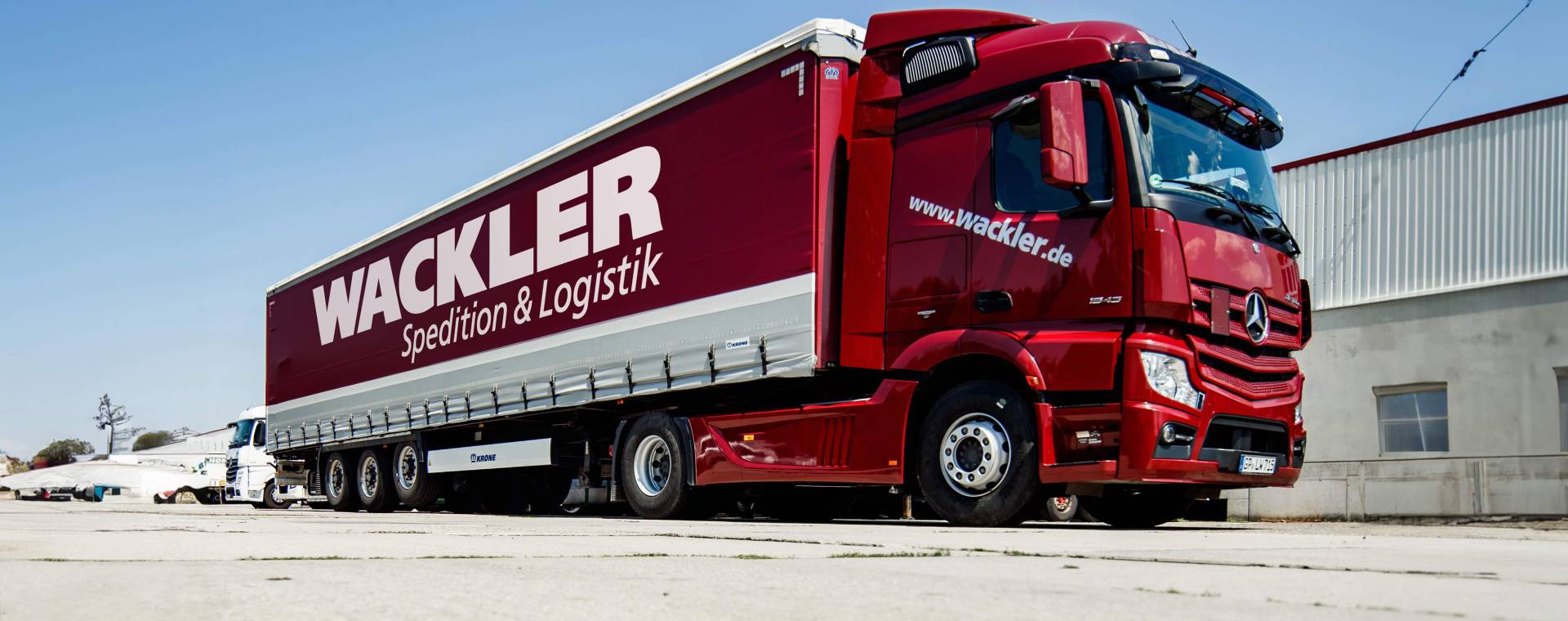
Digital upgrade for the logistics sector
Flexible transport logistics with IoT
Wackler success story
The Wackler success story
Simple and flexible transport logistics with IoT
Whether in warehouse management, transport or production, digitalisation is fundamentally changing logistics. Successful companies are focussing on transparency through networking to increase efficiency, competitiveness and customer satisfaction. In this issue of Business Cases, we show how the logistics service provider Wackler has digitalised and optimised its processes thanks to a simple solution.


Source: WACKLER
The Challenge
Easily connect hundreds of handheld terminals
In the logistics industry, processes must function quickly and smoothly. On-time deliveries and the associated high level of customer satisfaction are crucial for the competitiveness of providers. To ensure this, Wackler Spedition & Logistik uses around 300 handheld terminals, which the drivers of the transport vehicles carry with them. The terminals assign orders to the drivers and enable the recipients to track the goods they have ordered. The handheld devices are used to register the correct receipt of deliveries and to document damage claims.
The solution previously used by Wackler for the connectivity of the handheld terminals was based on mobile telephony with SIM cards from different network operators. However, this proved to be problematic, particularly in peripheral areas of the mobile phone networks, where reception was poor. Wackler Spedition & Logistik was therefore looking for a better solution for connecting its handheld terminals. The company therefore decided to use the managed SIM solution from Vodafone Business for this purpose.
Real-time transparency as a success factor
The Company
150 years of experience in logistics
Wackler Spedition & Logistik specialises in forwarding and logistics services and is part of the Göppingen-based Schwarz Group. The innovative family business offers its customers national and international transport solutions customised to their needs. It also has an extensive logistics portfolio, ranging from comprehensive warehouse management for a wide variety of industries to full-service and hazardous goods logistics and logistics solutions for e-commerce providers, including returns processing.
The company has over 500 employees at its sites in Göppingen, Baden-Württemberg, and Wilsdruff, Saxony. Wackler Spedition & Logistik has been active in the transport and logistics segment since 1846 and can draw on a wealth of experience.
The Solution
Digitalisation of handheld terminals thanks to IoT
Information exchange through handhelds does not generate large amounts of data, and communication with drivers usually takes place via text-based chat. Therefore, IoT-based communication proved to be a better solution for Wackler's needs compared to traditional radio data transmission. The IoT connection from Vodafone Business ensures reliable data transmission even under difficult radio conditions, such as in warehouses, depots or construction sites. If required, the handheld terminals can also use external networks via roaming. The terminals are also designed to buffer data and transmit it when the network connection is restored, so that incoming information is reliably delivered if there is a brief interruption in the wireless connection.
The management of the IoT SIM cards implemented by Vodafone Business was based on its managed SIM platform. This results in further advantages for Wackler, particularly in terms of organisation: Wackler can activate and deactivate the SIM cards in the platform dashboard as required, allowing the company to react quickly and flexibly to changing demand situations. The activation of new SIM cards, which previously took one to two days, can now take place without waiting times. In addition, the data volume booked by the company is distributed across the entire device pool - if more data needs to be transferred in individual cases, this is balanced out with other cases in which the transfer volume remains lower.
The entire solution impressed us with its simplicity.
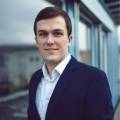
Marc Fiegert
Head of IT, Wackler Forwarding & Logistics
"Vodafone provides us with everything from a single source, enabling us to reduce our contractual relationships from several service providers to just one," reports Marc Fiegert, Head of IT at Wackler. "This reduces the administrative workload enormously. The solution also offers us complete transparency for each individual SIM card: we can see immediately which card is in which end device, keep track of individual data consumption in real time and can allocate our cost centres with a single click. Billing and the tariff model are also transparent, and the entire solution impressed us with its simplicity. What's more, with Vodafone we have a reliable contact partner for all our needs."
Digitalisation of handheld terminals thanks to IoT
The Advantages
At a glance
The lorry drivers' handheld terminals are connected to Wackler's scheduling and logistics system via the Vodafone Business IoT network. The company also benefits from a framework agreement with a simple tariff model that distributes the booked data volume across all devices in the pool. Wackler also praises the management of the SIM cards via the managed SIM platform as being much simpler compared to the previous solution.
Powerful, flexible IoT platform
with broad network coverage
Simple overview
in the user-friendly management portal
Extensive reporting options
thanks to digital data capture
Simple and fair billing model
allows distribution of the booked data volume
5 questions for Marc Fiegert

5 questions for Marc Fiegert, Head of the IT department at Wackler
"Improved connectivity is crucial"
As a division manager in the IT department at Wackler Spedition & Logistik, Marc Fiegert is responsible for the administration of the handheld terminals and their communication connection as well as for other connectivity requirements of the company. We spoke to him about the benefits of IoT and modern networking for the logistics industry.
Mr Fiegert, what advantages does the IoT connection of your drivers' handheld terminals offer?
Marc Fiegert: Switching from traditional radio data transmission to IoT communication has significantly increased the reliability of the radio connection. This allowed us to reduce our contractual relationships from several service providers to just one, namely Vodafone Business. On the IT side, the administration effort has been significantly reduced. We can add or deactivate SIM cards as our needs change. And the fair billing model, which allows us to distribute the booked data volume across all devices in the pool, gives us additional flexibility. This saves us several thousand euros in tariff costs per year compared to the previous solution.
By switching from classic radio data transmission to IoT communication, the reliability of the radio connection was significantly increased.
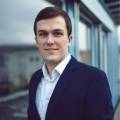
Marc Fiegert
Head of IT, Wackler Forwarding & Logistics
To what extent does the solution supplied by Vodafone bring you other practical benefits?
Marc Fiegert: The improved connectivity is of course crucial because it enables us to optimise our processes. And there are also some very welcome details. For example, we have discovered that the plastic from which the IoT SIM cards are made is more robust than standard chip cards. When the terminals are left in the vehicle at night in sub-zero temperatures in winter, this detail becomes a huge advantage.
Does the solution also have advantages in terms of sustainability?
Marc Fiegert: When logistics processes such as the short-term adjustment of routes function optimally, this shortens transport routes. This saves fuel and therefore greenhouse gas emissions and increases the efficiency of our processes.
How do you rate the cooperation with Vodafone?
Marc Fiegert: We are very happy to have a central point of contact for all our concerns. Vodafone Business absolutely understood our business and our requirements. Vodafone also has a great deal of IoT expertise.
What are the next steps in the collaboration?
Marc Fiegert: We are already talking to Vodafone about further projects as part of the ongoing digitalisation of our business. This also includes further areas of application for the IoT connection - for example in fire alarm systems. Other mobile applications such as backup connections for our telephone system are also being discussed. The big advantage would then be that we could book all of this within a single contract construct.
5 tips for Logistics 4.0

Optimise processes, reduce costs
5 tips for Logistics 4.0
The logistics industry is facing major changes: Digitalisation has the potential to optimise processes, increase efficiency and transform the entire supply chain. But where do you start when dealing with such a complex topic? In this article, we present five essential tips to help companies successfully integrate digitalisation into their logistics activities - and thus achieve Logistics 4.0.
Investing in the right technology
Choosing the right technology is the key to successful digitalisation in logistics. It is important that companies do not just focus on the latest trend, but rather on solutions that meet their specific requirements. Cloud computing, the Internet of Things (IoT), artificial intelligence (AI) and blockchain are just a few examples of technologies that can be used in logistics. Companies should carefully analyse their needs and then make targeted investments in technologies that improve their processes and make them fit for the future.
Integration of data analysis and management
Data is at the heart of digital transformation. The ability to collect, analyse and gain insights from data is crucial for success in the logistics industry. Companies should invest in data-driven solutions that enable information to be captured and utilised in real time. By integrating data analysis and management, companies can optimise their processes, identify bottlenecks and make informed decisions.
Automation of processes
The automation of processes is another key factor for digitalisation in Logistics 4.0. By using robotics, autonomous vehicles and automated warehouse solutions, companies can increase their efficiency and reduce costs. Automation makes it possible to eliminate repetitive tasks, reduce errors and shorten throughput times. Companies should therefore invest in automation technologies and integrate them into their logistics processes in a targeted manner.
Promoting a digital corporate culture
Successful digitalisation requires not only technological innovations, but also a change in corporate culture. Companies should promote a culture of openness, flexibility and continuous improvement. Employees must be trained in the new technologies and motivated to actively utilise them. It is important to create an atmosphere of change in which innovation and experimentation are encouraged. Only in this way can companies reap the full benefits of digitalisation and be successful in the long term.
Partnerships and collaboration
Digitalisation opens up new opportunities for partnerships and collaboration in the logistics industry. Companies should be open to cooperating with technology providers, start-ups and other players in order to expand their expertise and develop innovative solutions. By working together, companies can utilise synergies, share risks and jointly develop new business areas. It is important to build a network of partners that enables companies to benefit from the latest developments and trends in the industry.